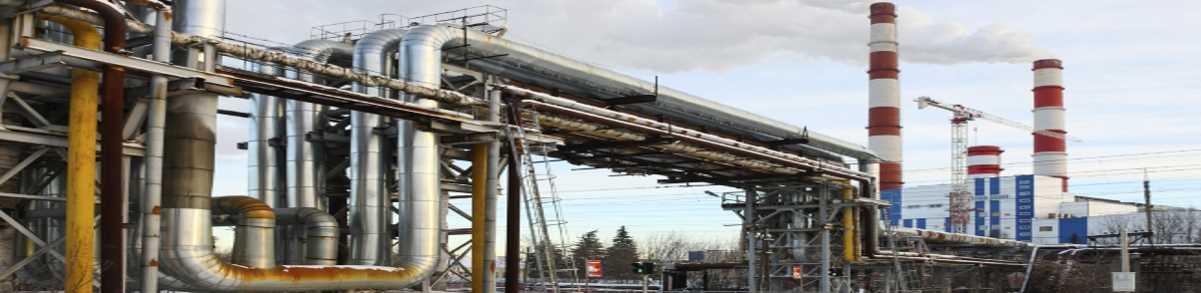
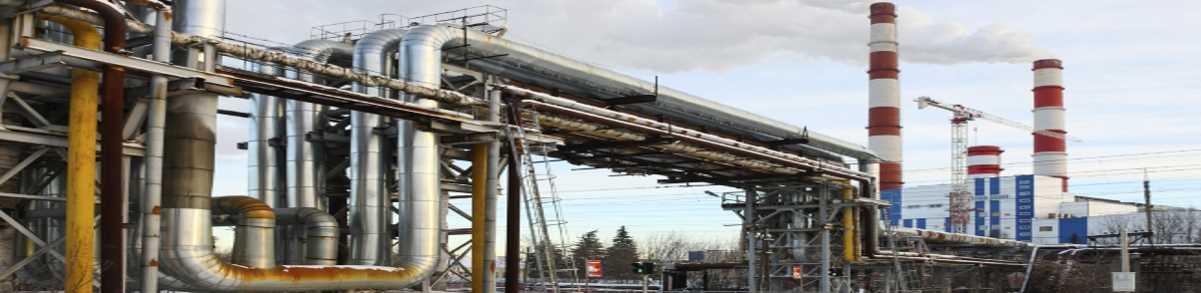
Condenser Water Flow Monitoring
Bionetics offers two approaches to measuring circulating water flow in steam surface condensers:
-
Total Flow Monitoring
This approach uses an engineered system that measures differential pressures in the piping to infer flow rate. This system is referenced in the ASME PTC 12.2 guideline, is recommended for all power generating facilities, and provides a practical and cost-effective approach to measuring total cooling water flow.
-
Single Tube Monitoring
The second approach uses a single tube instrument that measures flow and temperature. This system, also referenced in the ASME PTC 12.2 guidelines, is recommended for research purposes including determination of air binding, fouling, and condenser upgrade engineering assessments. To learn more about these unique instruments and their capabilities, contact us using the form on this page.
What Are the Benefits?
Monitoring circulating water flow can be an important tool to combat tube damage mechanisms. Debris fouling and the associated low flow velocity in the tubes it causes can accelerate pitting tube damage mechanisms. Flow is also an important parameter to measure for tube failures caused by microfouling-induced Microbiologically Influenced Corrosion (MIC). Actively monitoring circulating water flow for these issues can greatly reduce tube failures over the short and long term. An extensive study performed by Bionetics, in collaboration with Midwest Generation, Plastocor, and EPRI, is discussed in the following paper: Condenser Tube Circulating Water Flow Performance Monitoring & Troubleshooting at Midwest Generation Joliet Station.
Another area where total circulating water flow measurement is beneficial is for monitoring condenser fouling. An example where this measurement was instrumental in identifying a major fouling issue is summarized in the following article: Energy-Tech-May-2016-EKPC-Spurlock-Condenser-Fouling. Several Bionetics innovations and experience with the total flow monitoring approach described in this article includes design features that provide long-term reliable flow measurement.
This capability can be implemented as a standalone monitoring system or it can be an add on option for all RheoVac System owners. Major benefits of the system include:
- Most cost effective solution for monitoring total CW flow
- Measures flow per pipe
- Macrofouling (debris) quantification
- Automated purging for measurement taps (optional)
- Provides a critical parameter necessary for quality condenser performance monitoring programs
How Do They Work?
Differential meters use an obstruction in the flow path to create a differential pressure which can be measured. The calculations used to compute flow from differential pressure are based on the Bernoulli Principle which states that there is a relationship between the pressure in the pipe and the velocity of the flowing fluid. The primary differential producer used by the meter provides a restriction in the flow area that causes the fluid to accelerate. This acceleration can be computed by measuring the pressure drop across the differential producer. In power generation condensers, Bionetics selects an existing differential producer such as piping elbows and waterbox nozzles within the condenser for analysis to ensure that the signal produced will be adequate for the application and provide reliable flow measurement.
How Is The System Installed?
The installation process consists of installing taps during an outage and then installing isolation valves, fluid isolation diaphragms and differential pressure transmitters. The differential pressure transmitters are calibrated in the final configuration using accepted calibration methods such as a velocity traverse or a tracer dilution test. The transmitters are then connected to the RheoVac Condenser Monitor or the system’s central electronics for calculation of total flow and determination of fouling.
Due to the type of instruments used, these systems have a variety of analog and digital outputs available as well as standalone data storage. If the condenser is equipped with instrumentation that measures other bulk parameters such as shell temperatures and pressure, then the Condenser Monitoring System can provide complete health and performance monitoring of the condenser unit.
How Do I Add This Capability to My System?
Talk to us about adding this capability to your plant performance monitoring by using the form on this page to tell us about your system. You can also call us to discuss your requirements using the phone number at the top of the page or contact us via email on our Contact Us page.